|
|
|
Chemical Process Design Simulation
System |
|
|
|
|
|
|
CHEMCAD Chemical Process Simulation Software - Includes database of
chemical components, thermodynamic methods, and unit operations to allow steady state
simulation of continuous chemical processes from lab scale to full scale. |
|
|
|
|
|
|
CC-DYNAMICS Dynamic Process Simulation Software -
Takes your steady state simulations to the next level of fidelity to allow dynamic
analysis of your flowsheet. The possibilities are endless: operability check-out, PID loop
tuning, operator training, even online process control & soft sensor functionality.
The combination of two pieces of software, CC-ReACS and CC-DCOLUMN(which
may be purchased individually, if desired) make CC-DYNAMICS the dynamic simulator of
choice. |
|
|
|
|
|
|
CC-BATCH Batch Distillation Simulation Software - As an add-on or stand
alone program, CC-BATCH makes batch distillation simulation and design easy with
intuitive, operation step based input. |
|
|
|
|
|
|
CC-THERM Shell & Tube Heat Exchanger Design & Rating Software - As
an add-on or stand alone program, CC-THERM makes use of multiple international standards
for design and materials to make sizing your next heat exchanger faster and more accurate.
Rigorous designs are based on CHEMCAD's foundation of physical property and phase
equilibria data. |
|
|
|
|
|
|
CC-SAFETY NET Piping
& Safety Relief Network Simulation Software - A subset of CHEMCAD (all of
CC-SAFETY NET's features are included in CHEMCAD), this program allows rigorous analysis
of any piping network. We combine the latest in two-phase relief device calculation,
rigorous pressure drop calculation, rigorous physical property calculation and rigorous
phase equilibrium calculation to give you fast, accurate answers. |
|
|
|
|
CHEMCAD (Chemical Process Steady-State
Simulation Software) |
|
What
can you do with CHEMCAD? |
Increase
Productivity by Performing Everyday Chemical Engineering Calculations |
Maximize
Profitability by Designing More Efficient New Processes and Equipment |
Reduce
Costs and Capital Expeditures by Optimizing/De-Bottlenecking Existing Processes and
Equipment |
Comply with
Regulatory Agencies by Assessing the Environmental Impact of New or Existing Processes |
Leverage
Corporate Information by Maintaining a Central Database of Proprietary and Laboratory Data
|
|
|
|
|
How
do you actually use CHEMCAD? |
Draw your flowsheet |
Choose
your chemical components |
Choose
your thermodynamic model |
Specify
your feed streams |
Specify
your unit operations |
Run
your flowsheet |
Size
your equipment |
Investigate
cost estimate alternatives |
Assess
environmental impact |
Analyze
your results/Optimize and repeat as necessary |
Produce Process Flow Diagrams/Reports |
|
|
|
|
What are
some common application of CHEMCAD? |
Distillations/Extractions
(Batch & Continuous) |
Reactions (Batch
& Continuous) |
Electrolytic
Processes |
Thermo-Physical
Property Calculations |
Vapor/Liquid/Liquid
Equilibrium Calculations |
Equipment Sizing |
Heat Exchanger
Networks |
Environmental
Calculations |
Safety Analyses |
Cost Estimations |
Flare Header
systems |
Utility
Networks |
|
|
[Top of this page] |
|
|
|
CC-- BATCH
(Dynamic Batch Distillation Software) |
|
Why
should you use CC-BATCH? |
Short learning curve & very little
re-learning required |
Unique interface allows
intuitive set up of your batch distillation process |
Batch distillation
processes may be integrated into CHEMCAD flowsheets |
Rigorous use of built-in
thermodynamic models and themophysical property data |
Flexible flowsheet set up
and operational procedures allows most any batch distillation process to be simulated |
|
|
How
do you actually use CC-BATCH? |
Draw your
flowsheet |
Choose
your chemical components |
Choose
your thermodynamic model |
Specify
the column/charge/additional feeds |
Define
the operational procedures |
Run
the calculations |
Generate the
plots and reports |
|
|
What
are some common applications of CC-BATCH? |
Model existing
batch column equipment |
Explore
alternative processes for existing products |
Design
new equipment |
Validate
thermodynamics using laboratory batch column equipment |
Predict minimum
boiling ternary azeotropes quickly |
|
|
[Top of this page] |
|
|
|
CC--THERM
(Heat Exchanger Design Rating Software) |
|
It's
easy because it's a CHEMCAD program... |
If you know how
to use CHEMCAD, you know how to use 95% of CHEMCAD-THERM, so the usual new program
learning curve is virtually eliminated. Extensive help facilities are provided. Data is
entered using intelligent input procedures and dialog boxes. |
Throughout
the processing industry, it's a well-known fact that no other simulation programs come
close to CHEMCAD programs for ease-of-use. |
|
|
It's
easy because it's integrated... |
In heat
exchanger program, integration means accuracy, and accuracy starts with entering the
process data. Here's where you'll really appreciate CHEMCAD-THERM's full integration,
because process data is automatically transferred from CHEMCAD's flowsheets. |
Plus,
of course, automatic data transfer eliminated the tedium and invariable inaccuracies of
manual data transfer. |
Best of all,
CC-THERM uses the same Thermodynamics routines and physical properties databases as
CHEMCAD. the problems and inconsistencies that typically occur when processes are designed
using different programs are totally eliminated with CHEMCAD-THERM. |
|
|
It's
easy because the expertise is built in... |
Built-in
expertise means two things: First, CHEMCAD-THERM is rigorous and comprehensive. it's
designed to handle your most complex heat exchanger rating or design, and we mean the hard
problems. CC-THERM takes no short cuts, makes no assumptions, runs a full zone analysis
and stringent stream anlayses. And like all CHEMCAD programs, CC-THERM run fast. |
Second,
the program is intuitive in operation. Process engineers continually tell us how much they
learn about heat transfer analysis just by using CHEMCAD-THERM. With our HELP and our
step-by-step data input screens, you can have an exceptionally high level of confidence in
the accuracy of your rating or design. |
So whether you
work with heat exchanger problems daily or only occasionally, you'll enjoy that rare
combination of power and simplicity that comes with CHEMCAD-THERM. |
|
|
[Top of this page] |
|
|
|
CC--ReACS
(Dynamic Batch Reactor Control Simulation Software) |
|
From
experiment to production |
CC-ReACS's
flexibility makes it the ideal simulator at all stages of the design process, from
laboratory experimentation through scale-up, yield optimization, hazard analysis and
control. it can model vessels ranging from laboratory glassware or reaction calorimeters
to pilot or production scale reactors under a wide range of operating conditions. |
The
cost savings that can be achieved by improving the results of your pilot plant, or by
going directly from table top to full scale, can be significant. |
Special options
allow the chemical system to be separated from the plant model so the chemist can study
the behavior of the chemist can study the behavior or the reacting system under adiabatic
or isothermal conditions. Engineers can swiftly carry out scale-up calculations by
building upon this model. A wide range of alternative production routes and operating
strategies can be examined in detail, and extensive thermal safety studies can be
implemented. |
|
|
Technical
power |
CC-ReACS offers
an impressive list of features,which makes it possible to simulate almost any chemical
system in any reactor. This is accomplished by combining a unique interface which
understands the process chemistry with a sophisticated reactor model which contains
options for multiple jackets, internal and external coils, and heat exchanger. CC-ReACS
simulated batch, semi-batch or continuous reactor operation using a flexible sequencing
and PID control system. |
|
|
Reactive
distillation |
Together with
Chemstations' fully integrated dynamic distillation model, CC-DCOLUMN, CC-ReACS can
rigorously simulate combined reactor/distillation system. |
This feature
offers equilibrium based or mass transfer based simulation for packing and trays. This
powerful combination, CC-ReACS gives you a head start in tackling reactive distillation
problems. |
|
|
Kinetic
rate regression |
CC-ReACS rate regression facility
enables you to determine the rate parameters from imported experimental data. This data
can be any combination of temperature, concentration, volume or heat release data from as
many experiments as you have available. No other software package enables you to easily
fit this much data in s single run. |
|
|
[Top of this page] |
|
|
|
CC-DCOLUMN (Dynamic Distillation Control Simulation Software) |
|
CHEMCAD-DCOLUMN
is fast, accurate, applicable to a
wide range of processes, and easy to learn and use. It is fully integated with CHEMCAD,
which can perform steady-state simulation, equipment design, and DIERS
analysis. This allows you to move easily around and between
all aspects of your design. Only in such an |
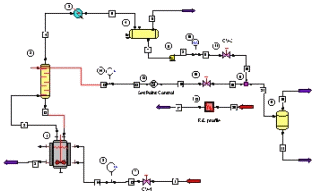 |
environment
can you achieve the really big paybacks the dynamic studies
can provide. |
Steady state simulation miss the dynamic aspects of process design such as operability,
the impact of disturbances, and many facets of safety issues. These are important
selection criteria for any process and the inability to fully underatand them generally
leads to over designs which cost millions of dollars in both capital and operating costs. |
|
|
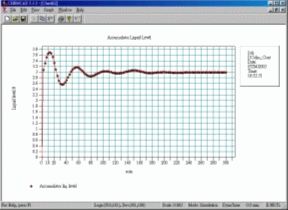 |
For example, from a steady-state viewpoint it is better to minimize holdup
in processing equipment. Holdup means larger equipment, which means larger fixed capital.
From an operational standpoint, however, holdup can make the difference between a smooth
working plant and an inoperable one. In operations, holdup means isolation from
disturbances, and may mean being able to run one section of the plant when another is
down. However, too much holdup means long process cycle-item causing corrections to
quality problems to take longer. So there are important tradeoffs. |
|
|
The abiltiy to
perform dynamic simulations means that these tradeoffs can be evaluated early in the
design before any decisions have been made. Thus, from the beginning you will be albe
to quantify the requirements of operability, control loop
tuning, changes in throughput or ambient conditions, safety
demands etc. This will save you money not just in capital
investments, but also in production costs. |
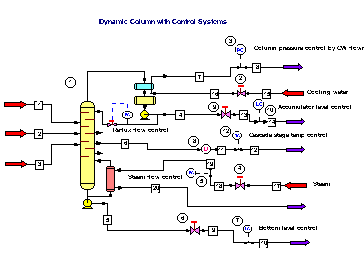 |
A plant which is designed with operability in mind can produce
considerably more than a plant where operability issues were
never explicity addressed. |
|
|
[Top of this Page] |
|
|
|
CC-SAFETY
NET (Piping & Safety Relief Network Simulation Software) |
|
CC-SAFETY
NET is an engineering software tool designed to
simulate the steady state behavior of pressure relief devices and piping systems under
actual flowing conditions. It also provides powerful facilities for environmental audits
in the prediction of volatile organic compound (VOC) emissions to atmosphere at
equilibrium conditions. |
|
|
 |
FLARE SYSTEMS:
CC-SAFETY NET
provides facilities for the design and analysis of flare
relief systems including all system components. These facilities include:
Simulation of the piping network including the blowdown drum. Flow can be vapor, liquid,
or two-phase, and critical flow is computed and limiting. |
|
|
|
Identification of the worst relieving case using case studies.
Optimization of the system using the of sensitivity analysis.
Sizing (and costing) of system equipment including pipes, relief valves, and pressure
vessels. |
|
|
The DIERS (Design Institute for Emergency Relief Systems) facility of CC-SAFETY
NET provides the user with the latest technology in the sizing and analysis of
safety relief vents in emergency situations. This technology is complex and difficult for
the average engineer to understand and apply. CC-SAFETY NET ensures that
you get reliable results because: |
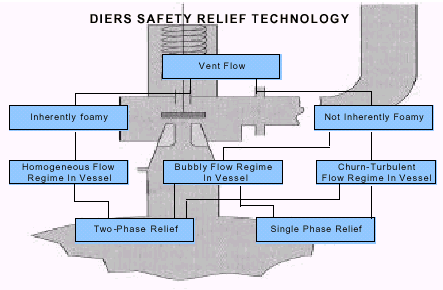 |
|
|
Chemstations has spent years studying DIERS and consulting with experts in the field. We
are thus able to provide you with a tool which is not only comprehensive and accurate, but
which also separates the useable from the purely theoretical providing you with a
practical, real world tool.CC-SAFETY DIERS facility has been used in the field for years. |
|
|
|
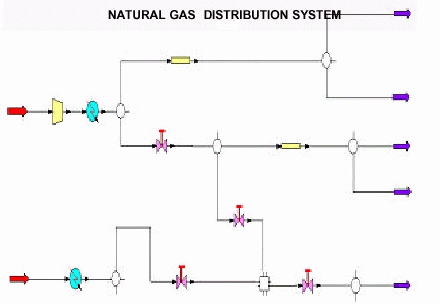 |
PIPING NETWORKS:
CC-SAFETY NET will simulate
any type of steady state piping network. Flow loops, distribution systems, and collection
networks can all be assembled and simulated in any combineation. These networks can also
include:
Pumps, compressors, expanders, valves, pipes, fittings, heat exchangers, and pressure
vessels.
Performance curves for pumps and compressors.
Critical flow restrictions. |
|
|
[Top of this
page] |
|
|